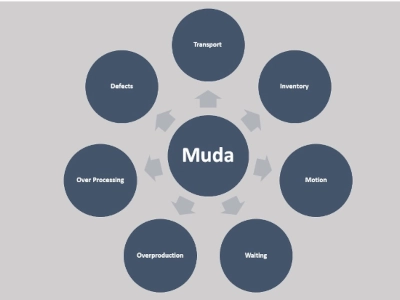
Muda is a Japanese term that means ‘futility, uselessness or wastefulness’, and is a key component of Lean Production and lean thinking.
A good example of Lean Production is the Toyota Production System, or TPS, which focuses on waste reduction at every step in the production process. Reducing waste is one way to increase profitability along with quality.
Customers expect a quality product or service and are willing to pay for it. A company or individual producing a product or providing a service can increase quality and have happier customers. Reducing muda, or waste helps keep costs to a minimum.
There are two distinct types of waste to be aware of for anyone providing a product or service to customers
- Waste that doesn’t add value but may be necessary to keep customers happy. For example, extra packaging to improve appearance, but not necessary to protect the product during handling and shipping.
- Waste that doesn’t add value and is unnecessary to keep customers pleased. These types of waste add to costs and should be found and removed.
One essential element of a lean process is to identify the activities that add value and those that don’t. Once identified, each process can be improved and refined to remove the activities that don’t add value.
The ‘father’ of the Toyota Production System, Taiichi Ohno, identifies seven areas of muda:
- Transportation - whenever a product is touched or moved during production can potentially be a source of damage or delay. Extra transportation doesn’t add value but does add cost and should be eliminated.
- Inventory - in any form, such as raw materials, in production (work-in-progress) or completed products usually represent a capital outlay that doesn’t produce cash flow. Time items are kept in an inventory status adds to waste and must be reduced to a minimum to keep products flowing.
- Motion - differs from Transportation because it relates to costs created during production. This includes wear on equipment and machines, equipment and machine downtime and injury to production workers.
- Waiting - refers to a product waiting to be processed through the production process or awaiting transportation to a customer. Speed of production determines how long a product is ‘waiting’.
- Overproduction - can be the costliest form of muda if a product is produced in large batches. Customer desires and preferences may change during the time it takes to make the product in large batches. Overproduction can lead to a high rate of waste through scrappage or write-offs.
- Over Processing - adding more steps to a production process means more time to produce the product while adding cost. Using more expensive parts or parts of a higher quality than needed to meet customer expectations are also examples of over processing.
- Defects - include any additional steps in a process that requires correction or reworking of a product to correct an initial defect.
In addition to the Seven Wastes identified in the Toyota Production System are:
- Misapplied or Unsused Skills - companies sometimes underutilize employee skills or create environments where knowledge and skills are not shared. Employees or departments operating within their own ‘silos’ are an example of misapplied or unused skills. Another example is having an employee performing a function they’re overqualified for or that could be automated. This muda is one that once eliminated, helps eliminate or reduce most other forms of waste.
- Confusion - a process isn’t written or clearly defined or lacks direction from management.
- Self Doubt - employees don’t believe they can produce a product or service within the given process. As Henry Ford once said: ‘You can think you can achieve something or you can think you can't and you will be right.’
What forms of muda or waste does your organization have?